Die Salznebelprüfung wird zur verschärften Korrosionsprüfung an Metallen und Legierungen herangezogen.
Den sehr hohen Schärfegrad der Korrosion verdankt der Salznebeltest der Bereitstellung eines hoch konzentrierten Elektrolyten, der die Korrosionsgeschwindigkeit maßgeblich beeinflusst. Der Schärfegrad der Prüfung hängt ab von der Salzkonzentration, der Prüftemperatur und der Prüfzyklusgestaltung.
Der Salzsprühtest wurde von einem Automotive Arbeitskreis entwickelt, um bestimmte Komponenten im Kraftfahrzeug unter verschärften Prüfbedingungen einem Lebensdauertest zu unterziehen. Die Prüfung dient vornehmlich zur verschärften Korrosionsprüfung an Metallen und Legierungen.
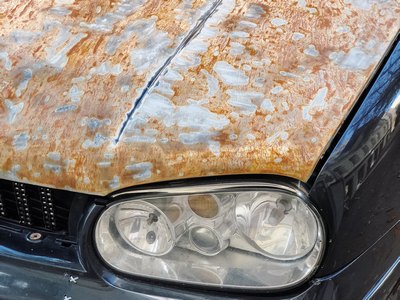
- ASTM B 117-73
- BMW GS 95024--3-1
- DIN EN 60068-2-11
- DIN EN 60068-2-52
- DIN EN ISO 9227 (ersetzt DIN 50021, DIN 53167)
- DIN EN ISO 9227 NSS
- DIN IEC 61701
- MBN LV124-2
- MIL-STD-810
- RTCA/DO-160
- VW 80000
Der Salznebeltest dient dazu, industrielle Werkstoffe auf Korrosionsbeständigkeit gegenüber salzhaltiger Atmosphäre zu prüfen.
Der bisweilen verwendete Begriff „Korrosionstest“ ist irreführend, da Korrosion ganz allgemeinen die Reaktion eines Werkstoffs mit seiner Umgebung bezeichnet, die eine messbare Veränderung des Werkstoffs bewirkt. Bei Metallen ist vor allem chemische Korrosion von Bedeutung (DIN EN ISO 8044; ehemals DIN 50900). Die wohl bekannteste Art von chemischer Korrosion bei Metallen ist das Rosten, also die Oxidation von Eisen. Beim Salznebeltest geht es nur um die korrodierende Wirkung, die durch Salzlösungen hervorgerufen bzw. befördert werden. Betroffene Gegenstände und Materialien sind vor allem im Fahrzeug- und Straßenbau anzutreffen (Salzstreuung). Insbesondere Automobile – aber auch andere im winterlichen Straßenverkehr eingesetzte Fahrzeuge wie Fahrräder oder Motorräder oder auch Rollstühle - leiden unter dem Einfluss von Streusalz erheblich. Nicht zu vergessen Bauelemente wie Stahlträger in Brücken oder metallene Leitplanken und ähnliches.
Das zu prüfende Objekt wird über eine festgelegte Prüfzeit hinweg in eine spezifisch ausgestattete Kammer eingebracht. Dort findet der eigentliche Test statt, indem der Prüfling kontinuierlich einer Nebelatmosphäre ausgesetzt wird, die einen bestimmten Salzanteil enthält. In aller Regel kommt Natriumchloridlösung mit einer Konzentration von 5% zum Einsatz, wobei ein PH-Wert von 6,5-7,2 eingestelltt wird. Die Umgebungstemperatur wird konstant bei 35 °C gehalten. So schlägt sich der salzhaltige Nebel kondensierend als Salzlösung auf dem Prüfling nieder und entfaltet korrosive Wirkung. Ziel ist es, unter Zeitrafferbedingungen weitaus längere Zeiträume zu simulieren. Dazu dient die hohe Salzkonzentration ebenso wie die hohe Temperatur. Dadurch beschleunigt sich der Korrosionsvorgang erheblich und auch zum Zwecke des Korrosionsschutzes aufgebrachte Schutzüberzüge werden zerstört bzw. verlieren ihre Wirkung. So korrodieren die Prüflinge tatsächlich erheblich schneller als unter normalen Alltagsbedingungen. Die Dauer der Tests liegt in der Regel zwischen 96 und 1000 Stunden, je nach Objekt und angenommener Lebensdauer. Jeweils nach 24 Stunden sollte der Prüfling entnommen und auf Korrosionsschäden untersucht werden. Am Ende der Testläufe sollen die Testobjekte mit entionisiertem Wasser gespült werden, um lose anhaftende, korrosionsbedingt entstandene Partikel zu beseitigen.
Daran anschließend sollte eine optische oder elektrische Analyse des getesteten Materials durchgeführt werden.
Soll beispielsweise die Wirkung eines metallummantelnden Korrosionsschutzes bewertet werden, so kann man diesen aus der Zeit ableiten, die das getestete Objekt bewältigt, ohne sichtbare Korrosionsspuren am Grundmetall aufzuweisen. Diese sind vor allem als Spuren von Rotrost erkennbar. Aus der Testanordnung einschließlich der Zeitrafferfunktion lässt sich schließlich die reale Schutzwirkung im Alltag ableiten.